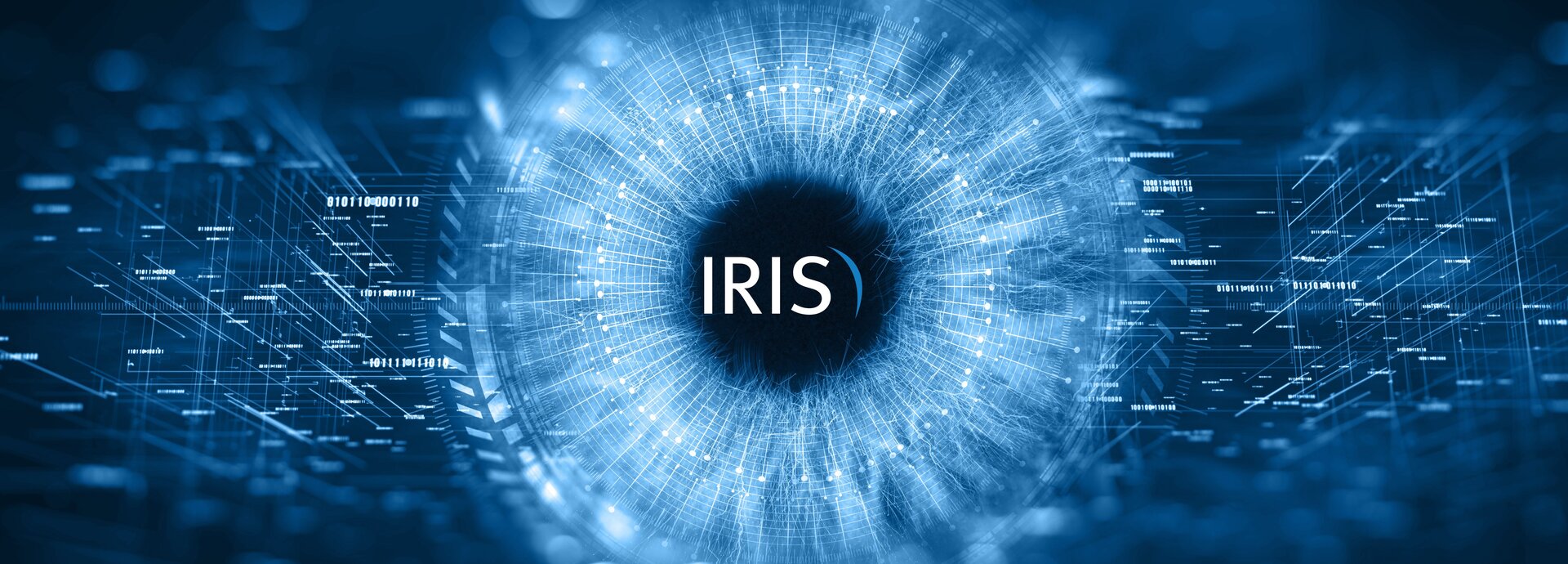
Digital Services
The MSF consists of an operations unit and a production unit. The operating unit is equipped with a small air-conditioned workshop and an office workstation. This unit also houses a material store, the micro-factory for manufacturing polymer parts, and a hand scanner for digitizing parts and quality control. The production unit is equipped with a Metrom PM700, a 6-axis hybrid machine. This machine combines additive manufacturing with Wire Arc Additive Manufacturing (WAAM) technology and CNC milling production. The MSF can produce metal parts with a maximum size of Ø 500 mm x 450 mm. The current focus is on selected stainless steels. In other applications, all weldable wires can theoretically be used.
The unique combination of welding and CNC capabilities of the MSF allows for fast and location-independent production of spare parts. In addition, essential subsystems such as power generators, compressed air generators and more are already integrated into the MSF.
The Micro-Factory can produce polymer parts with a maximum size of 300 mm x 200 mm x 270 mm. The FDM technology allows a wide range of materials to be used, including PLA, PA6, TPU, ABS, ASS and PETG (some with micro carbon fibers).
What makes the MSF smart is its integration into the collaborative IRIS® platform. As an OEM of military vehicles, Rheinmetall understands the importance of secure data transfer and lifelong fleet management, including maximum quality assurance. The cloud-enabled IRIS®platform enables fully integrated operation of the IRIS®assist and IRIS®fleet software applications with the MSF and meets IT security standards for data processing up to VSnfD. IRIS®print is the digital interface and stores all relevant information about the printed component and issues a digital product passport to ensure system security.
Flexibility and speed in the provision of spare parts are the results achieved through the use of additive manufacturing in service. This emerging manufacturing process is used for prototyping, low-volume production and manufacturing support. In addition, a wide range of services such as engineering support is offered. Rheinmetall also conducts research in the field of additive manufacturing in cooperation with civil and military universities, institutes and industrial partners.
The contract manufacturing supported by RLS in the aftersales sector encompasses various types of work. In addition to the production of initial prototypes and installation samples for pre-development, mock-ups and installation aids for series production are regularly produced. Another application of contract manufacturing is obsolescence elimination. This is where spare parts are required that are either no longer available or would take too long to deliver using conventional production methods. In this case, RLS Aftersales either uses the production technologies available in-house (e.g. Mobile Smart Factory®) or works together with a partner company. There is no restriction on a particular manufacturing technology, but the most suitable manufacturing process is selected based on the particular use case - from polymer to metal.
Additive manufacturing follows a different manufacturing strategy to conventional manufacturing, so simply copying a part is not always practical or economical. For this reason, RLS Aftersales also offers various services in this area. These include engineering support (development services), in which component enquiries are technically evaluated, parts adapted to the design if necessary, optimised and prepared for additive manufacturing (design for additive). As a systems house for the parts in question, Rheinmetall is demonstrating its strength as a partner for the additive manufacturing process, particularly in the area of design for additive.
Since additive manufacturing is still a comparatively young technology and is constantly evolving, RLS Aftersales is also pursuing a research mission. It constantly monitors developments in the market (technology scouting), investigates new applications and participates in selected research topics. RLS Aftersales always pursues the goal of developing technology in a customer and user-oriented manner. The research projects therefore range from basic research to process optimisation and much more.
IRIS®suite is a product family based within an IT ecosystem designed to maximise the technical and economic effectiveness and efficiency of maintenance processes. The individual product modules are seamlessly integrated to enable maintenance and usage. The IT ecosystem backbone, IRIS®platform, enables data processing up to the VS-NfD (NATO RESTRICTED) level of confidentiality. The applications that utilise IRIS®platform include IRIS®fleet, IRIS®assist, IRIS®print and IRIS®diagnostic.
IRIS®fleet serves as a solution for the creation and maintenance of a digital CV for each equipment with interfaces to ILS databases, ERP systems and the monitoring of configuration statuses. IRIS®assist provides the technician a digital working environment for maintenance processes based upon the interactive use of electronic technical documentation. IRIS®diagnostic supports guided diagnostics digitally in direct connection with equipment in order to provide IRIS®suite with status and usage data.
IRIS®platform is the multi-client, infrastructural cloud for software applications such as the fleet management system (IRIS®fleet) and other Rheinmetall applications. Rheinmetall thus provides a platform for hosting modern, containerised applications that follow modern software architecture paradigms such as self-healing, scalability and automatic failover.
The IT solution can run air gapped on the customer’s network and be administered by the customer themselves or be provided as a Platform as a Service (PaaS). The IT solution is contained in a private edge cloud and, when required, without remote access from IT partners nor Rheinmetall. The Private Edge Cloud complies with ISO 27000, BSI C5 and can therefore host data with security level VS-NfD (NATO RESTRICTED).
IRIS®platform is a based within a Kubernetes cluster architecture, i.e. all services are operated in several Kubernetes clusters.
The Rheinmetall Fleet Management System (IRIS®fleet) is a fully integrated and collaborative software solution for managing and maintaining military equipment fleets and holdings life cycle data. The solution enables cost-efficient fleet management to aid high availability. IRIS®fleet can also serve as a collaboration platform between customers and Rheinmetall to exchange fleet information.
The solution consists of a database platform (IRIS®platform) and a web-based fleet management application. IRIS®fleet offers the customer central access to maintenance, configuration, availability and field data for the entire fleet, for each individual equipment down to and including sub-assemblies. The customer secures intuitive MTBF (mean time between failure) analysis, spare parts consumption, usage profiles, etc. By using IRIS®fleet, lifecycle costs can be significantly reduced and equipment availability can be notably increased.
IRIS®fleet can be utilised on Rheinmetall's IRIS®platform or hosted on a customer's network. Alternatively, each IRIS product can be hosted using container orchestration, regardless of platform.
IRIS®fleet also forms the basis for condition monitoring, condition-based maintenance and artificial intelligence (AI) supported predictive maintenance. IRIS®fleet organises and structures all relevant life cycle data, including HUMS data, per equipment and sub-component.
IRIS®assist is an on- and offline solution designed specifically for equipment repair technicians, allowing users to work interactively with technical publications (IETD including IPC) and support the management and implementation of the following maintenance tasks examples:
- Interactive use of technical publications with an intelligent HTML viewer (S1000D Interactive Electronic Technical Documentation (IETD) Viewer)
- Interaction with spare parts catalogues
- Add, edit and perform maintenance tasks
- View and record each technician's work record
- The use of digital checklists to guide the execution of inspections and repairs
- Reporting on equipment status
- Photographic, video and audio documentation
- Entering and uploading field and usage data
- Build configuration monitoring (BZÜ) updates
IRIS®assist ensures media-free data transfer between the technician and the fleet manager/supervisor utilising IRIS®fleet.
In addition, IRIS®assist minimises errors and standardises the quality of repairs through intuitive and user-oriented digitalisation of repair processes including automatic data transfer.
IRIS®print is an on and offline IRIS®platform tool that is a multifunctional software solution for the additive manufacture and management of spare parts utilising Mobile Smart Factory® (MSF). IRIS®print is not only a digital warehouse for all relevant production data for the manufacturing process, it also supports inventory management and creates digital product passports for 3D printed parts.
In addition to CAD models and drawings, additive manufacturing often requires additional files such as G-code or the correct welding parameters for the WAAM process. In IRIS®print, this information is stored clearly and securely for each part. The integrated stock management option also makes it possible to link the materials and tools required for the production of each component. This optimises the production process and reduces preparation errors. Additionally, spare part profiles can be created for storing print and component quality as well as other information.
With IRIS®print and IRIS®fleet combined, it is also possible to access Rheinmetall certified parts via "pay-per-print". A serial number can be automatically allocated to a component, allowing it to be efficiently tracked. Maintenance intervals can also be linked to the manufactured part. Other functions of this combined use include license management for MSF components and a purchasing function for consumables and spare parts for the systems integrated into MSF.
IRIS®diagnostic is an advanced solution to aid technical system fault diagnostics.
The combination of the external test system, integration of third-party maintenance and diagnostic software including license management, a simulation module for generating equipment specific signals and operating status and the integration of technical documentation is the basis for efficient fault diagnostics.
IRIS®diagnostic operates within a secure IT environment ensuring secure data transfer. Real-time transmission enables reliable and rapid communication between various applications in IRIS®suite.
An integrated knowledge database supports fault diagnostics through logically guided tests and utilising fault tree analysis.
In addition, the maintenance computer provides comprehensive insight into the supported equipment system.
The display of the Interactive Electronic Technical Documentation (IETD) supports the user in fault diagnostics and functionality testing.
With our IRIS Data Analytics tools, the user is ideally equipped to meet all challenges and can work effectively and efficiently.